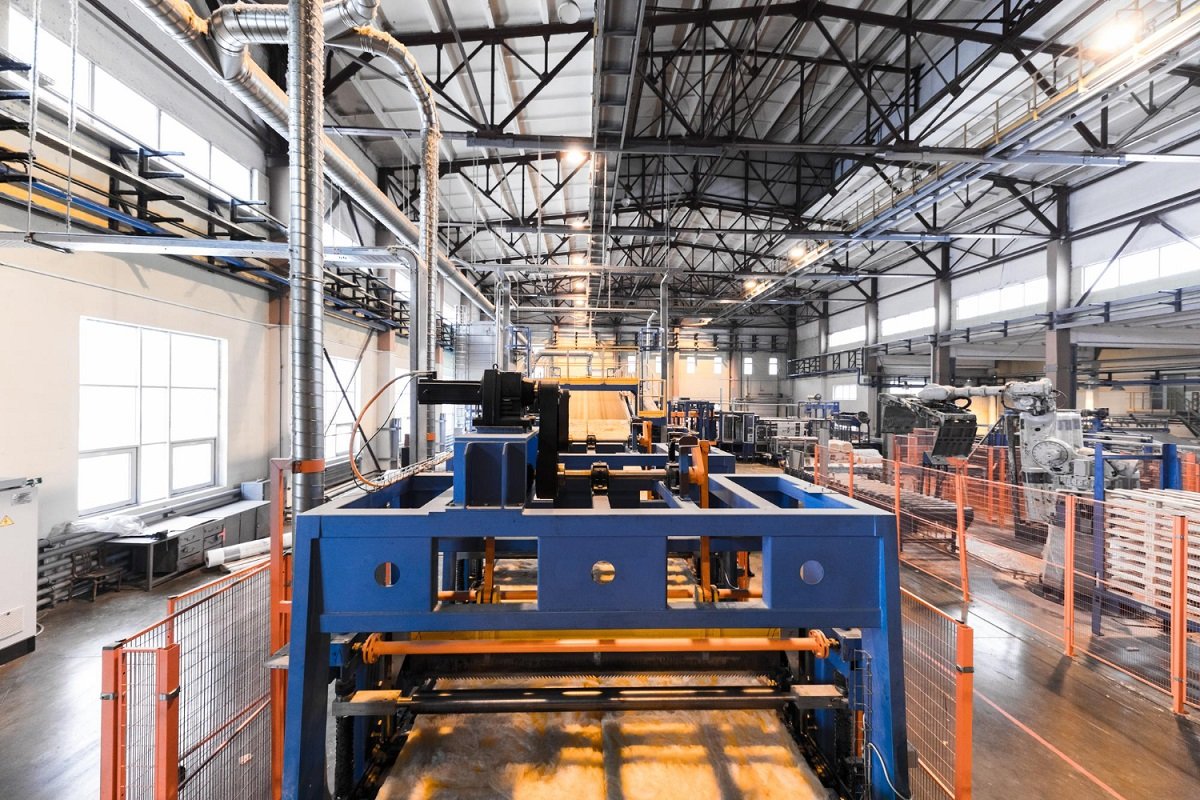
Metal sheets consume dimensional space, that is why they need to be rolled into cylindrical, conical or curved shapes to save warehouse space. To make this happen we utilize an automatic plate rolling machine. These machines find application across various industries like construction site, automobile factories, aircraft making companies and many more.
The “automatic” feature ensures minimum manual intervention because the machine is provided with computer controls or programmable logic controllers (PLCs) to ensure the rolling process.
It facilitates high-speed production without compromising accuracy, which makes it perfect for mass production. Advanced models offer features like multiple pre-set bending programs, variable roller speeds, and auto-alignment for added functionality.
How Is an Automatic Plate Rolling Machine Manufactured?
An automatic plate rolling machine requires a labour of love during the manufacturing process. It passes through many critical stages before becoming a work of art in final form. Starting with the design and engineering stages, detailed blueprints and simulations using advanced CAD software are produced in order to achieve precise operational requirements.
Subsequent material selection considers durable materials, such as hardened steel and cast iron, which ensure durability and resistance to wear under high-pressure operations. In the machining and fabrication stage, rollers, gears, and hydraulic cylinders are machined using CNC milling and turning to ensure high precision.
In the assembly process, these members are assembled and put together by electrical, hydraulic, and automation systems into an overall strong structure, aligned as well to permit smooth operation and finally tested or calibrated on this machine to allow it to execute its performance effectively, accurately in conformity with specified safety standards toward any industrial application.
Related: Applications and Manufacturing of Sheet Metal Press Brake Machines
What Quality Control Measures Are Used in Manufacturing Automatic Plate Rolling Machines?
Quality control is crucial for the performance, reliability, and durability of an automatic plate rolling machine. Key quality control measures are material testing wherein the components undergo hardness, tensile strength, and wear as well as corrosion resistance tests, which ensures the durability of the machine.
Advanced measuring tools verify dimensional accuracy of critical parts like rollers and gears. Load testing replicates real conditions to ascertain whether the machine can work with the predefined material thicknesses and pressures. It conducts rigid tests on automation systems and controls to ensure a smooth process.
Safety tests verify that emergency stops and covers of protection do meet all industry norms. Performance testing includes putting the machine into operational modes with diverse speeds and loads, thus determining consistent performance with accuracy in a real-life application.
Related: How Press brake manufacturers optimize bending operations?
How to Select the Right Automatic Plate Rolling Machine?
There are various important factors involved in the selection process of the right automatic plate rolling machine. Starting with material specifications, you may need a machine that can process the specified kinds and thicknesses of materials to be used in your operation.
In bend accuracy, machines with advanced CNC controls and pre-set bending programs can help you meet high-accuracy requirements. Production volume is another consideration; for high-volume production, machines with automatic material feeding and rapid cycle times are ideal.
Ensure the size and workspace of the machine fit within your facility while meeting your production demands. Consider automation features like customizable options and user-friendly interfaces to enhance productivity and reduce operator workload.
The reputation of the manufacturer matters; choose well-established manufacturers that offer warranties, strong customer support, and easy access to spare parts. Finally, weigh out the budget and ROI by making the initial investment justifiable through long-term efficiency, less labour, and minimal maintenance costs.
Related: USA’s Best Investment Casting Suppliers: Sinking the Gap between Innovation and Reliability
Conclusion
Automatic plate rolling machines are of paramount importance to modern fabrication industries. They have the ability to offer precision, efficiency, and versatility. Thus, it is essential to know about their functioning, manufacturing, quality control, and selection criteria in order to harness the benefits.
In aerospace, construction, or other industries requiring superior bends, only the right machine will do. It will yield consistent performance and superior results for you.